Innovations in artificial intelligence for methanization
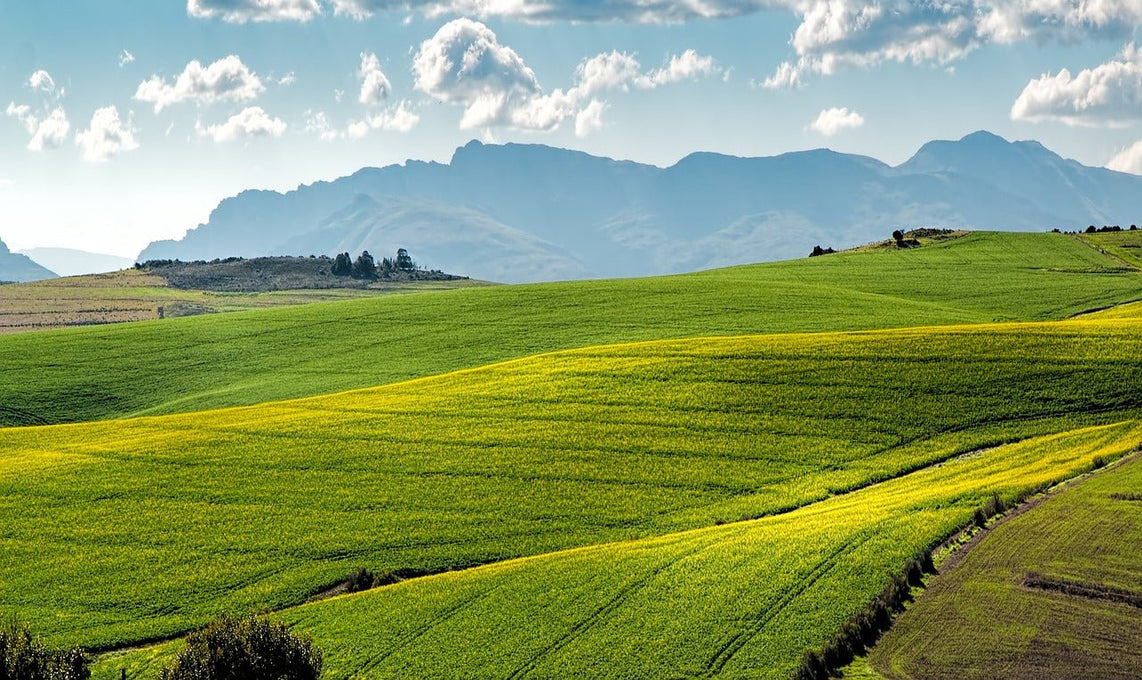
Innovations in artificial intelligence for methanization: how AI improves the monitoring and performance of methanizers
Anaerobic digestion is a complex process that transforms organic waste into biogas and digestate, requiring optimal conditions for efficient and sustainable production. The rise of artificial intelligence (AI) has opened new perspectives to optimize and automate this biogas production, bringing significant improvements in the monitoring and performance of methanizers. In this article, we will explore how AI is revolutionizing the methanization sector.
1. Optimization of the digestion process
The methanization process relies on biological degradation of waste, influenced by many parameters such as temperature, pH, substrate composition, and biomass levels. AI, particularly through machine learning, can analyze massive amounts of data to identify optimal operating conditions. Machine learning algorithms can adjust critical variables in real time to ensure optimal biological degradation, reducing retention times and increasing biogas yield.
Example: By analyzing historical data, an AI model can predict necessary adjustments based on waste composition and temperature variations, thereby improving the energy efficiency of the methane digester.
2. Failure prediction and prevention
One of the main challenges for Methane plant operators is to ensure continuous operation without costly interruptions. With AI-based predictive maintenance systems, it becomes possible to detect early signs of failure and intervene before a problem occurs. AI uses data from sensors to identify patterns that indicate wear or impending malfunction. This approach reduces maintenance costs and prevents unplanned shutdowns.
Example: An anomaly detection algorithm can alert operators when a motor or pump begins to show signs of weakness, allowing intervention before a failure occurs.
3. Improving the quality of biogas
AI can continuously analyze the quality of the biogas produced, automatically adjusting conditions to maintain an optimal composition. This is particularly useful for maximizing methane yield and minimizing the production of undesirable compounds like carbon dioxide and hydrogen sulfide. AI models can also detect trends that affect biogas quality based on the types of substrates used, allowing for precise adjustments.
Example: When receiving a new batch of biowaste, the AI system can automatically adjust the digester conditions to ensure that methane production remains stable.
4. Automated real-time control
Methane digesters equipped with IoT (Internet of Things) sensors can transmit data in real time for automated control. AI models process this data instantly and adjust parameters to keep the digestion process in optimal condition. AI can also adapt conditions based on variations in biowaste supply, allowing for great flexibility.
Example: A digester receives more waste than usual? AI can increase the temperature or adjust the pH automatically to compensate for the increase in organic matter.
5. Predictive analysis of biogas production
AI can predict biogas production volumes based on biowaste input streams. This allows operators to plan activities in advance, including biogas collection and storage, to meet energy needs or demands of existing infrastructure. By knowing in advance how much biogas will be produced, it is possible to optimize the logistics, storage, and even sales of biogas, creating a smoother and more efficient workflow.
Example: By knowing the chemical composition of a batch of biowaste, AI can predict that the biogas generated will have a higher methane content, allowing its use to be optimized according to energy needs.
6. Environmental data management
Methane digesters have a direct impact on their environment, and AI can help minimize this impact by monitoring emissions and adjusting operations accordingly. For example, by tracking levels of CO₂, odors, or potentially harmful emissions, AI systems can alert operators if thresholds are exceeded and even suggest solutions to correct the situation. This not only helps meet environmental standards, but also improves the sustainability of facilities.
Example: If sensors detect an increase in H₂S emissions, AI can trigger corrective actions, such as adjusting oxygen levels in the digester.
7. Integration of AI in training and decision support
AI can also be used to train operators and help them in their decision-making. Augmented reality systems or simulators can offer real-time training scenarios, reproducing complex situations and allowing operators to gain experience without risks. Operators can also receive automatic recommendations based on data analysis, making the management of methane digesters more accessible and less prone to human errors.
Example: A new operator can use an AI-based simulator to understand the effects of different parameters without risk to the real methane digester.
Conclusion
Innovations in artificial intelligence provide effective solutions to the challenges of methanization, enabling intelligent monitoring and continuous optimization of performance. Thanks to AI, methanizer operators can not only improve biogas production, but also reduce costs and minimize the environmental impact of their facilities. As these technologies continue to evolve, methanization will become even more efficient, reliable, and environmentally friendly, positioning AI as a key player in the energy transition.